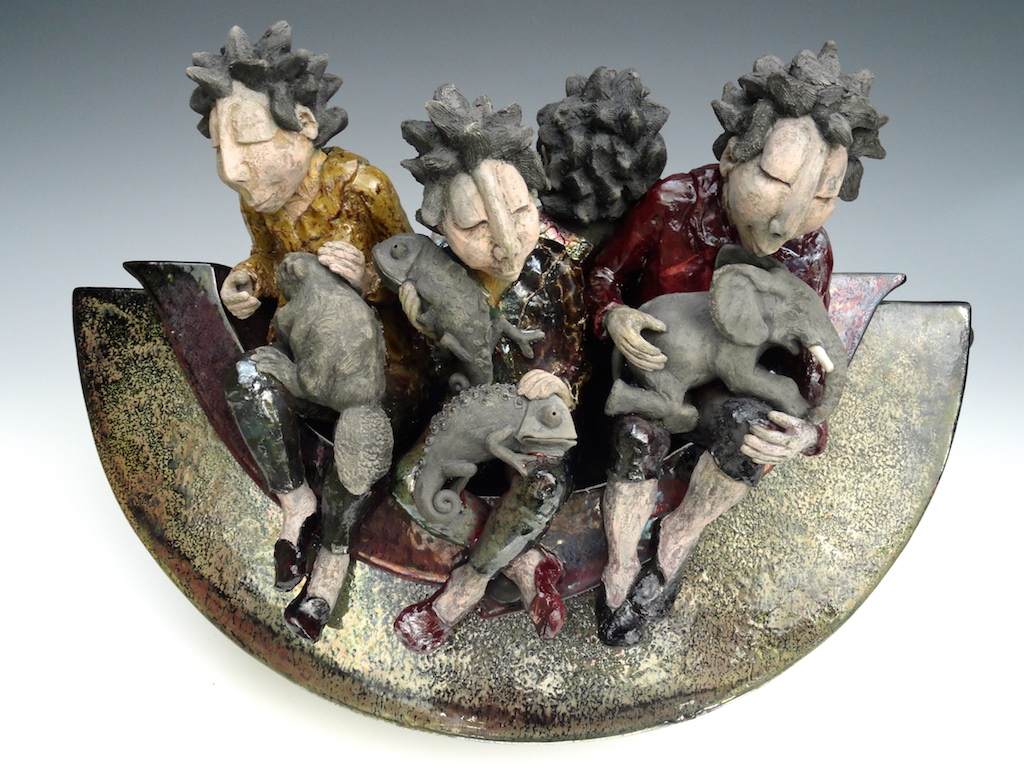
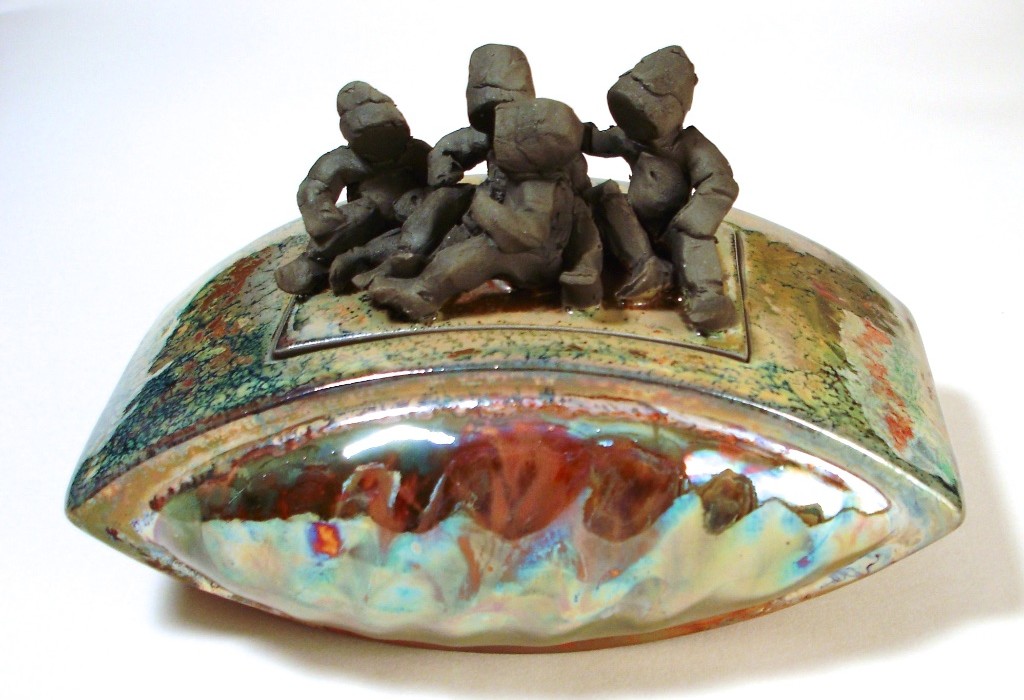
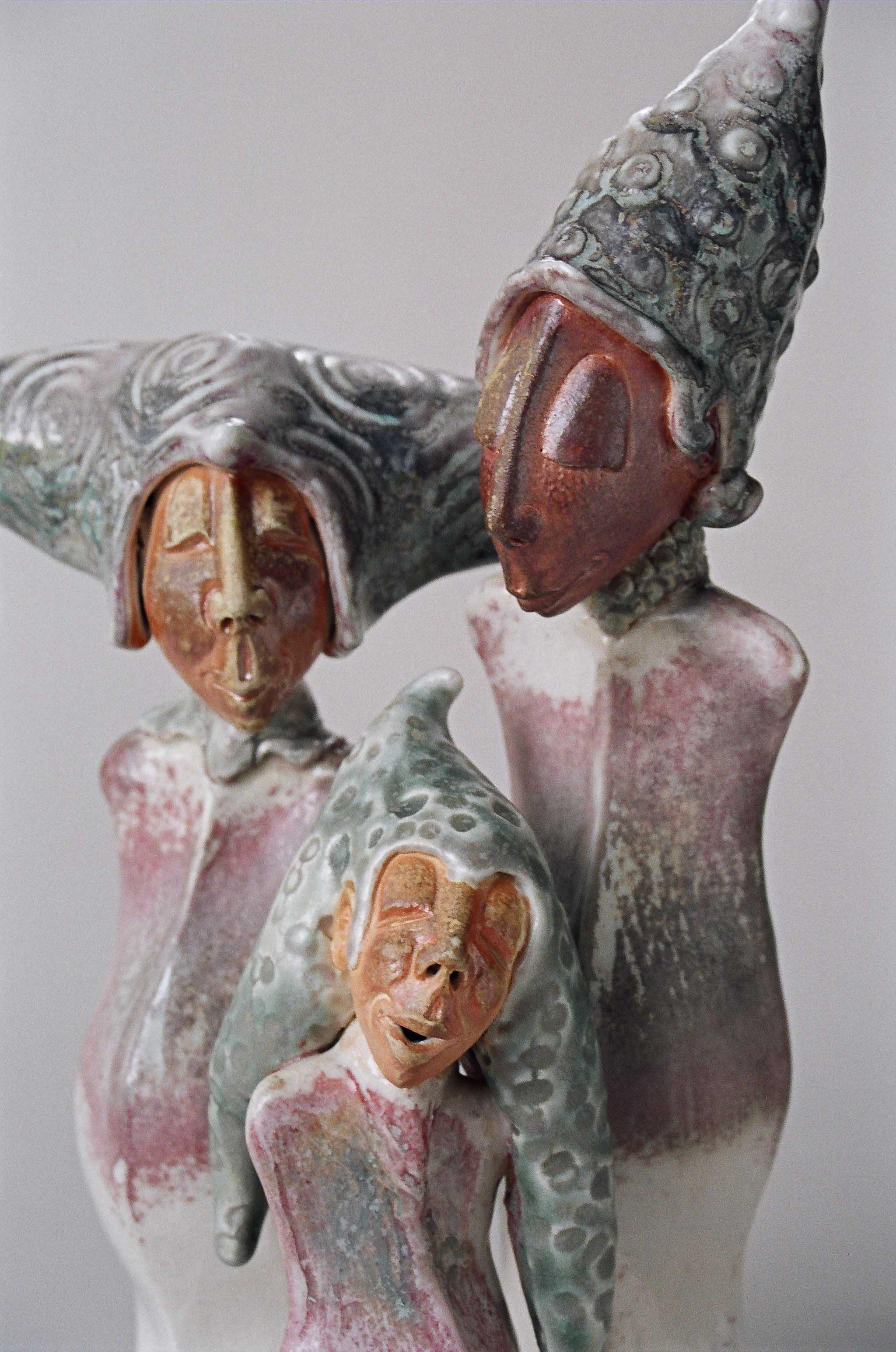

Raku Firing
Raku is a Japanese technique invented in the 16th century for producing tea bowls for Japanese tea ceremonies. The western world has modified the original technique slightly.
Raku is the second firing of the piece, whereby it is heated up to 1000-1100 degrees Celsius, at which temperature the glaze is melted on the surface. The piece is then pulled out of the kiln with long tongs and placed in a container filled with combustible material like sawdust, newspaper, dried leaves etc. These materials ignite right away. Closing the container creates a reduction atmosphere whereby the carbon, which comes from the combustible material, first becomes carbon monoxide and searches for more oxygen in order to become carbon dioxide. Due to a lack of air, the oxygen is taken from the metal oxides contained by the glazes. The metallic sheen and flashing colours are the result of this reduction process.
There is also another important reaction that happens. In the smoke filled reduction chamber, the carbon penetrates into the clay body creating the beautiful crackles for which Raku is known. It also transforms the unglazed surfaces into a nuanced black.
Wood firing
Wood firing is at the very root of civilization, ever since humans first began to understand how fire hardened clay. Before discovering fossil fuels, coal, oil, later propane, and electricity, people were using wood to fire clay objects like simple figures, bowls, storage jars, and clay tablets etc
In a wood kiln, ash from the fire box falls on the ceramic pieces melting and reacting with the surface on both glazed or unglazed pieces, forming a thin layer of natural glaze. This makes the clay more water retentive.
My work is sculptural: wood firing lends a distinctive look to them that feels very different from the raku finish.
Bronze
My pieces are cast in a foundry using the “ lost wax method”